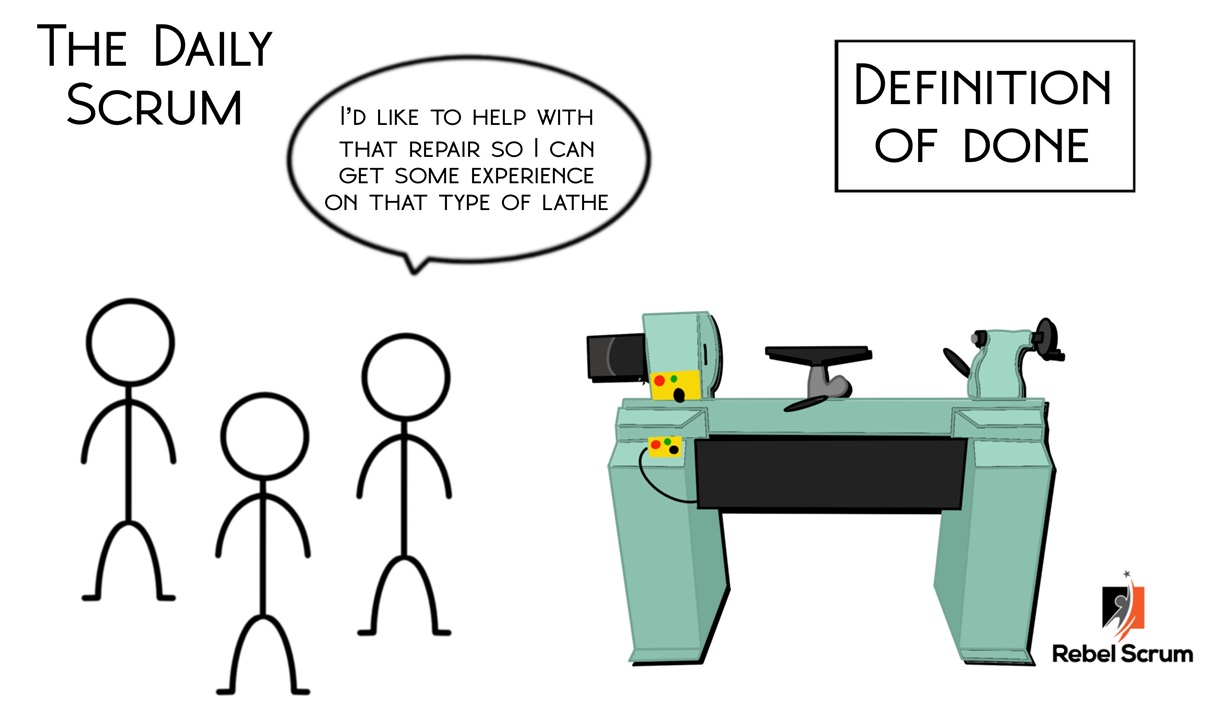
At Argus, the maintenance team in Edmonton faced a challenge: ensuring consistent, high-quality repairs while dealing with an unpredictable workload. The Edmonton team, responsible for maintaining over 60 CNC lathes, mills and MTM's, found that inconsistencies in their process led to frustration. Tasks like ordering replacement parts or cleaning up after a repair were sometimes overlooked, causing unnecessary delays and friction among team members.
Brayden Yundt, Maintenance Manager, introduced Scrum as a framework to bring structure and transparency to their work.
Maintenance in a machine shop is unpredictable. The team never knows what issues will arise or what skills will be required. To handle this, they introduced a one-week sprint cycle and a Tuesday refinement meeting with leadership to prioritize upcoming projects. They also started thinking in terms of planned vs. unplanned capacity, dedicating only 75-80% of their time to scheduled work while keeping the rest open for unexpected tasks.
The result? A more accountable, communicative, and efficient team.
Benefits of Scrum for a Maintenance team
The two most useful impacts of adopting Scrum, according to Brayden, have been the Daily Scrum and the team's ownership of the Definition of Done.
At the Daily Scrum, the team—a mix of mechanical and electrical repair experts, including millwrights and electricians—found that a structured check-in helped them align their tasks for the day, balance planned and unplanned work, and foster on-the-fly upskilling for newer staff.
But easily the most helpful impact has been the team's ownership of a Definition of Done. Previously, friction could easily arise when team members didn’t follow the same standards for completing repairs. Some would leave behind an unclean workspace, while others forgot to order replacement parts, shifting the burden to their teammates. By establishing a 15-point repair checklist, the team ensured that "done" meant more than just making the machine operational—it included cleaning up, documenting the work, and restocking used parts.
"The Definition of Done sets the standard we expect to work to and holds us to that standard."
Having the team create their own Definition of Done has been one of the most significant improvements. Having a manager come in and do something like this could have produced resistance, but when the team themselves owns their own Definition of Done, it's something that they are all committing to. And that makes all the difference.
Here's what team members are saying:
"The Definition of Done sets the standard we expect to work to and holds us to that standard", says one of the maintenance team members.
"It holds me accountable", says another.
"The Definition of Done has become more robust and useful than I could have anticipated", says Brayden Yundt, Maintenance Manager. "The team has really embraced this concept, and it has reduced frustration and rework."
Why is this so useful?
The team's Definition of Done includes things like resetting machine parameters, something that is easy to forget. Other elements include simple reminders to document the work that was done or to order replacements for any parts used during the repair. These reminders are helpful, and because the Definition of Done is something that is owned by the team it is viewed more positively than a procedure documented by leadership.
Conclusion
With the Edmonton team seeing tangible improvements, the next step is expanding this Scrum-based maintenance system to Argus' Nisku location, where the team is responsible for over 50 CNC saws, lathes, and mills. By fostering accountability, reducing low-level conflicts, and creating a shared understanding of quality, Scrum has helped this maintenance team operate with greater efficiency and professionalism.
As Brayden Yundt and his team continue to refine their approach, one thing is clear: defining what "done" really means has transformed their way of working—for the better.
******
Rebel Scrum is the host of the annual Scrum Day Madison conference, scheduled for October 16, 2025. This year's theme is Small Steps to Big Value.